科学者・研究者・研究開発者の職種紹介や転職情報など、理系キャリアに関する情報をお届け。
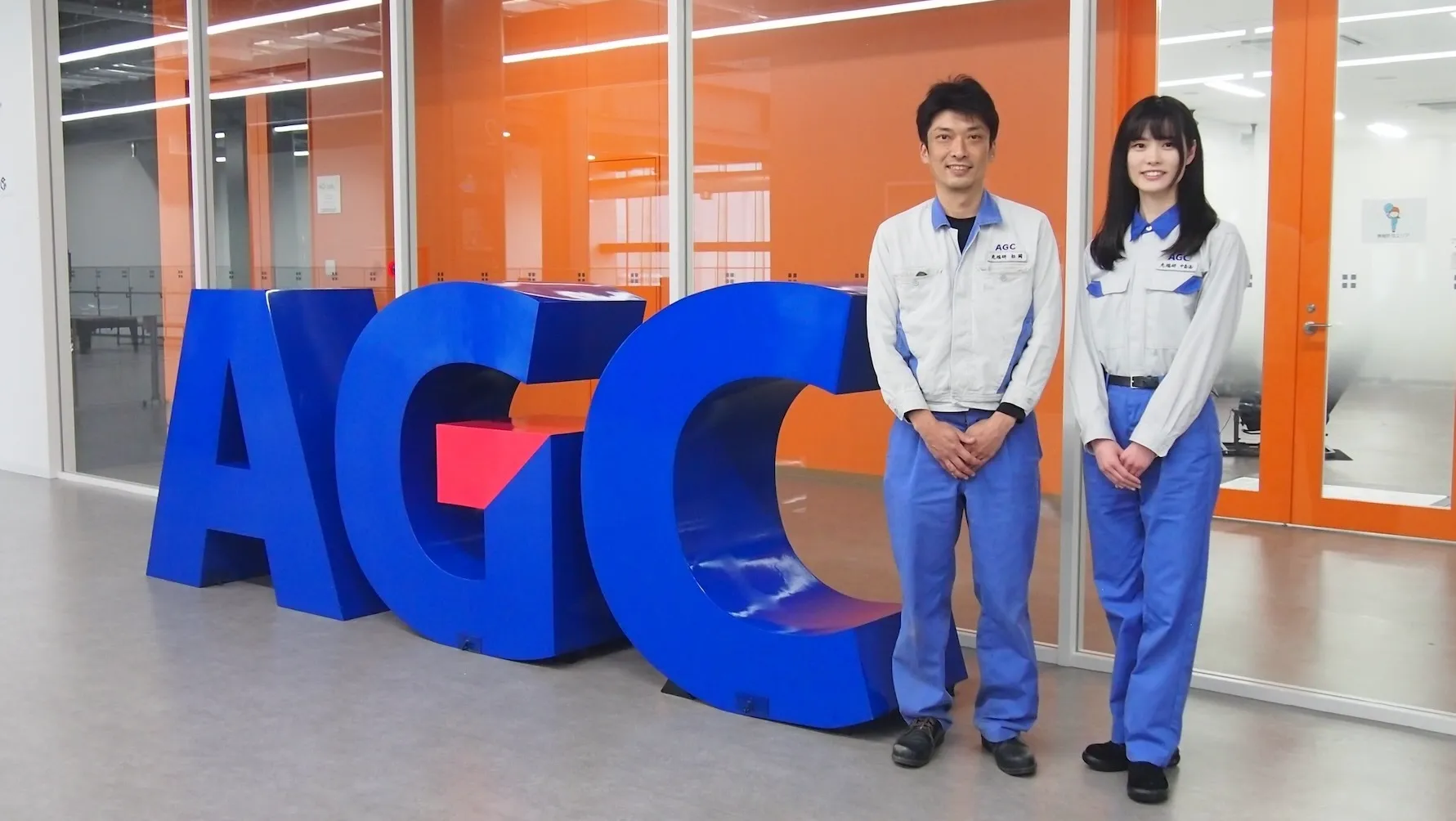
職種名や求人情報を見ただけでは「仕事の内容がよくわからない」「イメージできない」ということ、ありますよね。知っているようで意外と知らない“理系の仕事“にフォーカスし、その仕事で活躍している先輩に詳しい内容を教えてもらおう!というのが「理系の職種紹介」シリーズです。
第4回目のテーマは「物性評価』の仕事について。
材料の物性を正確に把握することは、安全で性能の良い製品を産み出す基本であり、ものづくり企業において、すべての活動の基盤となる仕事です。 今回取材に伺ったのは、世界最大級のガラスメーカーとして知られるAGC株式会社、横浜テクニカルセンター。ガラスを製造する装置に使う各種部材の評価を担当されている松岡瑞樹さん(2010年入社)と中島あゆ美さん(2022年入社)に、お仕事内容や、やりがいなどについて教えていただきました!
AGC株式会社
1907年(明治40年)設立。旧社名・旭硝子株式会社。建築用ガラス、自動車用ガラス、ディスプレイガラスに代表されるガラスの製造・販売で世界トップクラスのシェアを占めるほか、電子材料、化学品、セラミックスなど幅広い領域でグローバルに展開する日本を代表する総合素材メーカー。
AGCの研究開発体制
まず、AGCにおける研究開発体制について整理しておきます。
AGCでは、材料、プロセス(製造工程)、設備の開発を担う技術本部と、製品開発を担うカンパニーの開発部門が連携し技術開発を進めています。AGCの事業領域はガラス製品だけでなく、電子材料やライフサイエンスまで大変幅広いので、領域ごとのカンパニーに分かれて製品開発が行われていますが、どの事業にとっても共通で基盤となる基礎的な研究を技術本部で行っています。
技術本部の中でも、今回お邪魔した先端基盤研究所は、サイエンスにもとづく原理追求を進めながらも、ものづくりの量産の現場に展開しうる最先端の基盤技術を開発することがミッションです。ガラスの溶解/成形/加工プロセス技術、有機・無機ケミカルプロセス技術、更には分析・評価、シミュレーション技術、IT技術など、将来にわたってAGCを支える基盤となる技術を開発しています。
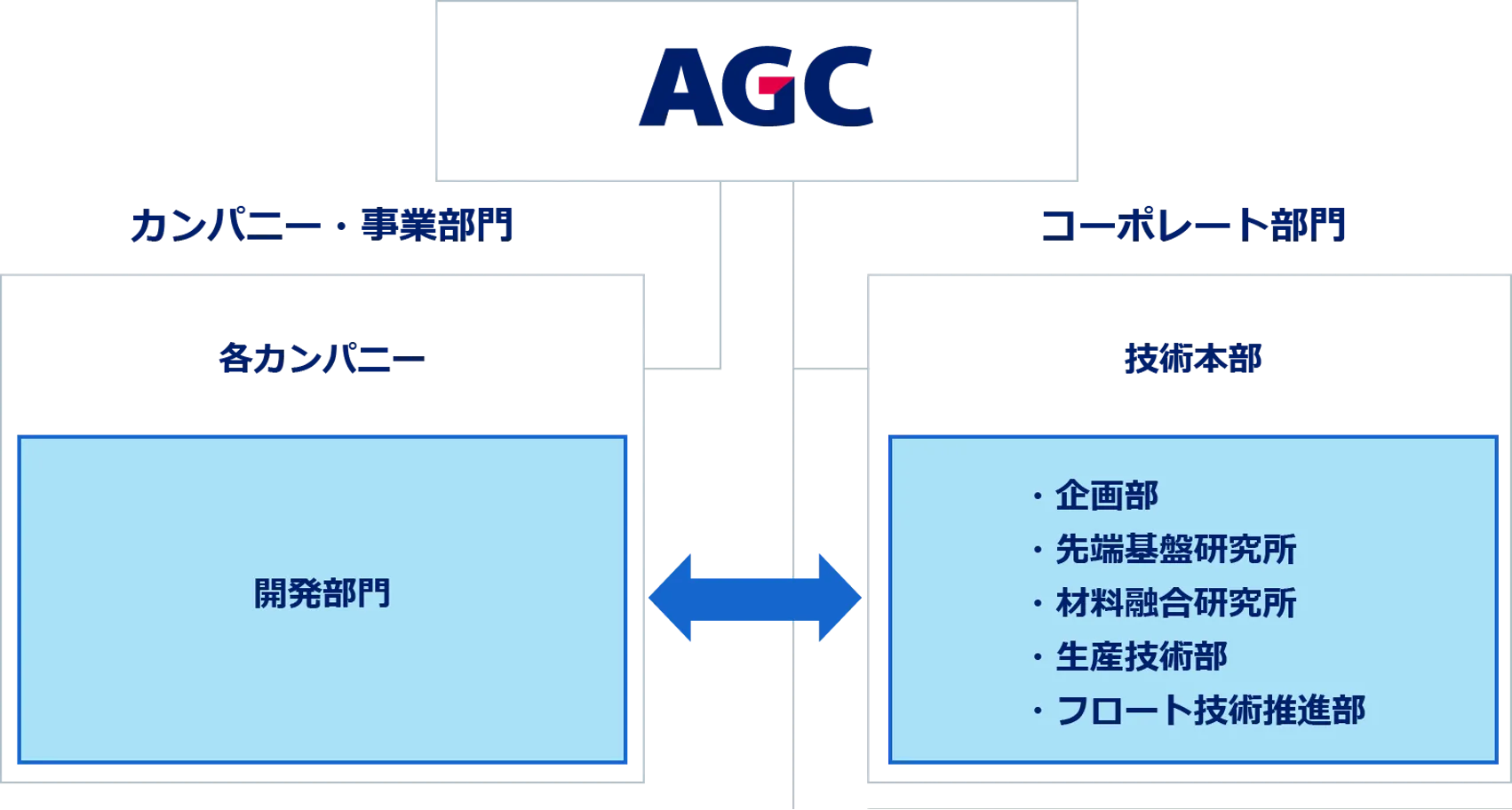
タップして拡大
画像提供:AGC株式会社(https://www.agc.com/innovation/organization/index.html)
今回お話を伺った松岡さんと中島さんが所属するのは、先端基盤研究所内の「共通基盤技術部」。共通基盤技術部では「評価」「分析」「シミュレーション」という3つのチームがあり、お2人は「評価」のチームに所属し、ガラスの製造工程で使われる部材(ガラス製造設備の各種部品)の評価を主な仕事とされています。
ガラスといえば、材料を高温で溶かして成形するかなり特殊な環境で作られるイメージです。使える材料も限られそうですが…、いったいどういった研究が進められているのでしょうか。
それでは早速仕事の詳細ややりがいについて、伺ってみましょう!
ガラス製造過程における物性評価の仕事とは?
ガラスの製造設備に使用する部材を評価し最適な材料を選定する
入社14年目・松岡さんの主な業務
・ガラス製造設備に使用される金属、セラミックス、炉材の評価と分析
・製品品質向上のほか、設備の寿命延長、コストダウンを目的とした最適な材料選定や表面処理の検討
・高温、あるいは特殊環境下で使用される材料物性、寿命の評価、適用可否判断、材料選定
・リーダーとしての後輩の育成
松岡 私たちの所属する共通基盤技術部の評価チームは、ガラスの製造設備で使用される部材の評価開発を担当しています。
ガラス製造は非常に高温で行われるため、製造設備に使用する部材も当然ながら高温に耐える材質であることが必要です。耐熱性だけでなく、特殊環境下でも化学的に安定していて、腐食に強い材質であることなども求められます。
具体的には高温環境に耐える金属部材やセラミックスなどの素材が主な評価対象になることが多いです。ガラスの製造設備は数年から十数年の単位の稼働を想定しています。その長い年月が経っても、これらの素材が「そもそも本当に使えるのか」「寿命はどれほどか」「耐食性は充分か」といったことについて十分な実験と分析を行い、最適な素材を選定していきます。評価は、実験室から実機に近い環境まで、様々なスケールで実施します。
もし評価に誤りがあって、予想より早く部材に問題が起きたら、最悪の場合設備が壊れる可能性もある、とても責任重大な仕事です。設備の安全稼働のほかにも、製品品質の向上や生産コストの改善など、製造設備の部材の選定は、ものづくりにおいてとても大切な役割を担っています。
入社2年目・中島さんの主な業務
・セラミックス材料のプロセス開発
・ガラス製造設備に使用される金属、セラミックス、炉材の評価と分析
・ガラス欠点解析
中島 私も基本的には松岡さんと同じ、材料の強度や耐食性の評価をしています。設備に使う材料が、ガラス製品の欠点にならないようにするのが目的です。適さない材料を使うと不純物混入の要因になることがあります。製品中に生じた欠点を、様々な装置を使って分析し、素材の問題や製造時の温度といった原因を特定します。個人で担当するテーマもあれば、チームで取り組んでいるものもあります。
松岡 評価は、新規設備のためばかりではなく、既存の設備で行うこともあります。新規の設備に対しては、先ほどお話ししたように材料的な観点で最適な手段を検討するための評価がメインですが、現在使っている製造設備については、あと何年使えるかという判断のために評価を行うことが多いですね。耐用年数は、例えば稼働後に蓄積したデータを分析することで大まかに予想できます。また、稼働中に予期せぬ不具合が生じた場合にその原因を調査するための評価を行うこともあります。工場や他の部署と協力して、必要に応じて現場での対応にもあたります。
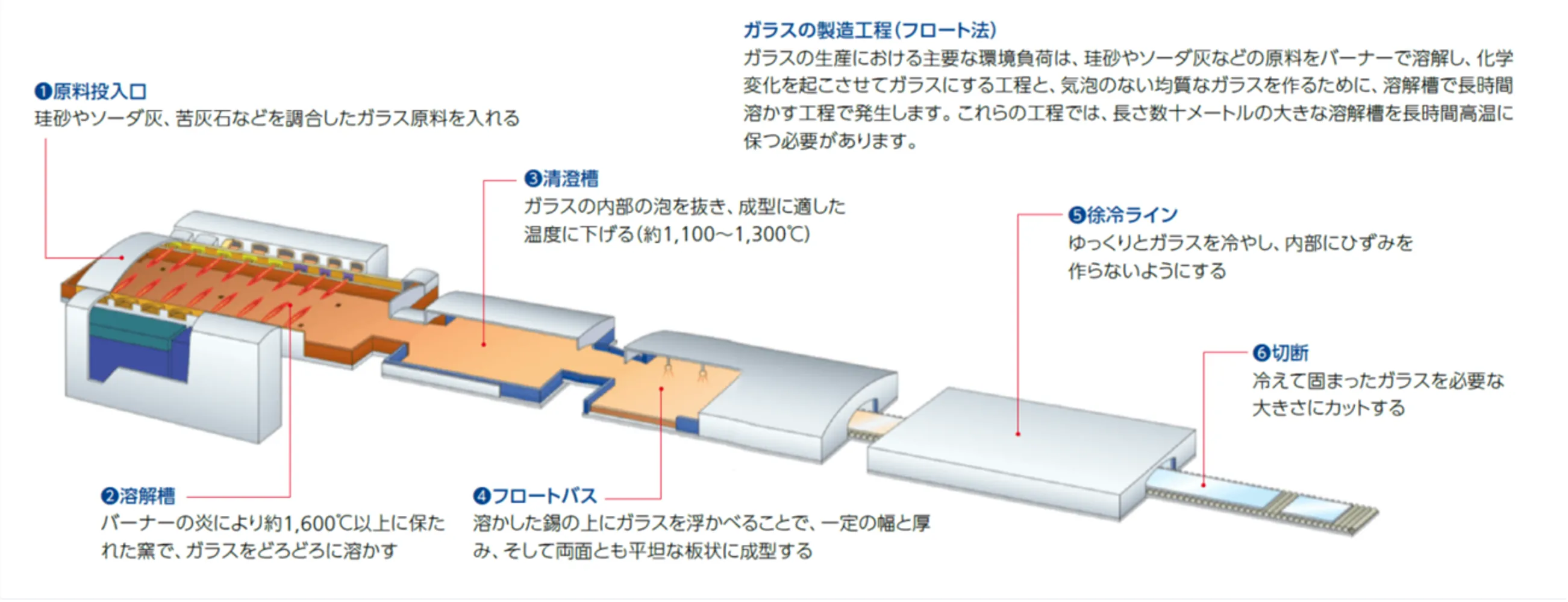
タップして拡大
▲ガラスの製造工程(プロセス)の一例。工程ごとに目まぐるしく変わる環境下に対応する設備部材の選定と開発には、技術の粋が集められている。
画像提供:AGC株式会社(https://www.asahiglassplaza.net/sustainability/development_re/)
仕事のやりがいと魅力について
醍醐味は「新しい評価技術を開発すること」
松岡 仕事のなかでも特にやりがいを感じるのは、新しい評価技術の開発です。当社では次々と新しい用途のガラスや新しい製造方法が開発されていますので、設備の部材もその都度新しいものにアップデートする必要があります。製造工程(プロセス)の安全性を保つための条件設定や、部材寿命の評価、コストダウンなど…検討事項はたくさんあります。
中島 昨年、ガラス製造設備に耐えうる炉材の評価で、高温下での強度を確保しつつ、コストを下げるにはどの炉材がいいのかを検討するテーマに携わりました。実際に使われる環境を模擬して、候補部材を試験したのですが、たくさんの実験を経て、適する炉材を事業部の方に提案できたときは、達成感を感じることができました。そのような経験を一つでも多く重ねていきたいです。
松岡 作りたい製品に対していい設備や設備部材が世の中にまだ「ない」という場合もあります。そういうケースでは他部署の協力を得ながら、環境に適した材料系を検討することもします。材料の酸化や腐食に対して新しい表面処理技術を開発したりもします。
外部の企業やアカデミアとの共同研究も積極的に行っています。最先端の技術を取り入れながら新しい評価技術の構築に役立てたり、特にまだ社内でニーズが顕在化していなくても、世の中に出た新しい部材を先に調査したりすることもあります。
ガラスは建物から半導体までいろんな製品に使われています。最先端のガラスをつくっているからこそ、その評価法も社内で開発しなければなりません。前例のないものを確立することは大変難しい仕事ですが、それを考えるのはとても面白くやりがいがあります。
もともとは新素材の開発がやりたくてAGCに入ったのですが、それはほかの職種について知識がなかっただけで、いまでは評価の仕事がとても気に入っています。良い製品を作るために新しい手法を開発し続けることは、ものづくりの根幹に関わることだと感じます。単に材料の物性を評価するのではなく、評価を通じてより良いものづくりを可能とするのが物性評価を担当する我々のミッションです。私たちの開発した評価技術は、ガラス以外の領域でも応用されることがありますし、それを知るととても嬉しく誇らしい気持ちになりますね。
評価の仕事の難しさとは
完全に同じ環境を再現できない中で、どうやって評価する?
松岡 評価の仕事で最も難しいと感じるのは、実際の現象を実験で再現し、そのメカニズムを正確に評価する初期段階です。実現象の模擬の構築ですね。このステップを間違えると信頼性が大幅に低下します。現象を完全に正確に再現できないことも珍しくないですし、小規模な実験とスケールアップした実機では、全く異なる結果が出ることも多いです。問題が生じた際は、その原因とメカニズムを何度も検証し、改善策を模索します。模擬できているところとできていないところを正確に見極める必要があるのですが、それはかなり難しいことです。色々な製品において経験を積み引き出しが増えると、考察の確度が上がってきます。
個人で判断しようとしても知識の蓄積には限界がありますので、いろいろな人と話して総合的な判断をすることが重要だと実感しています。
中島 実験室で実際の工場での現象をどこまで再現させられるかは、確かにとても難しいです。また、複数の事業部の製品の製造プロセスについて、並行で様々な評価を実施していかなければなりません。膨大な数の材料について、知識の習得はかなり大変ではありますが、いろんな製品に関わるので学べることが多く、そこで使った評価技術を他で活かすことができるようになれば、自分もレベルアップできると感じて頑張っています。
松岡 部材の寿命についても、実際にその年月を実機と同じ環境で観察できるわけではありません。これもデータを蓄積することである程度判断がつくようになってきますし、文献を読んで過去の知見を参考にすることも多いです。
評価者として成長するために
中島 私は入社して現在2年目になります。コロナ禍での入社だったので、最初は対面でのコミュニケーションの機会が少なかったり、工場実習に行けずに設備を見る機会が持てず、イメージがわかないまま評価をしなければならなかったりしたことが難しかったのですが、最近は各地の拠点に行くことも増え、またガラス製造設備の知識もついてきて「こういう実験をすれば、こういうことがわかるんじゃないか」という感覚がつかめてきました。製造プロセスの評価において、実際に現場に足を運んで設備を目で見て学ぶことの重要性を痛感しています。
AGCでは若手の頃には先輩社員からサポートを受けます。個人で取り組むテーマ、チームで行う研究テーマを与えてもらい、評価手法や実験計画の立て方、報告書の作成など一連の流れを先輩社員の指導を受けながら経験します。そうして取り組んだテーマは最終的に、研究所長にプレゼンテーションします。こうして業務の一連の流れを習得していくことができます。また事業部門の方々とのコミュニケーションの取り方もサポートを受けながら経験を積むことができます。
また、社内研修だけでなく、過去資料を見たり、外部のセミナーや学会、講演会に参加して新しい測定技術を学び、社内のみなさんに共有したりするなど、主体性をもって業務に取り組むことも心がけています。みなさん丁寧に教えてくださいますし、自分がつまずいている部分について相談しながら進められていて、とても働きやすい環境だと思います。
研究職を目指すみなさんへ、学生時代にやっておくとよいこと
松岡 私の場合、大学院の専攻は今の仕事とは全く異なり、特に金属とは無縁でした。その経験からお話しすると、知識は入社後に学べるので、学生のうちは、論理的な思考力を磨くことがなにより大切だと思います。専門は何でもよいので、とにかくメカニズム的なところを論理的に考える訓練を学生のうちにたくさんしておくとよいと思います。卒業して研究職に就いた際は「こうなったときは何が起こっているから、こういう評価をした方がいい」といった研究の作戦を、いろんな選択肢を持って論理的に考えることができるかどうかがとても重要です。うまくいかないときどうするか、粘り強く考えられる人が向いていると思います。
中島 大学の研究ではゴールがはっきりしていることが多いですが、実際の仕事では目標や方法が途中で変わることがあります。会社に入ってからは、松岡さんのおっしゃるように、状況を的確に把握し、論理的かつ柔軟に対応する方法が求められると強く感じます。一度で解決することは稀で、予定通りに進むことは少ないです。そうした状況でどう対処するか、地道な思考と対応が必要だと思います。
松岡 また、仕事は個人で行うものではなく、社内外いろいろな方とのかかわりの中で課題を解決していくものです。常に論理的に考え「自分はこう思う」と、いろんな方と建設的に意見交換できる素養を養うことがなにより重要だと思います。
これからの目標について
中島 私の目標は、特定の評価分野において「中島に聞けば解決する」と認識されることです。共通基盤技術部に属する以上、一つの製品で磨いた評価技術を他の分野にも応用できるようにしたいと考えています。自分が見つけた何かの技術が、他の分野でも使われるようになったら嬉しいですね。
松岡 私の目標は、評価技術全般において、分野を問わず頼りにされ、期待される存在になることです。特定の部材だけではなく未経験の部材分野においても、松岡に聞けば一緒に考えてなにかしてくれるだろうという期待感を持たれる人ですね。また最先端の材料技術に明るいという信頼感を持たれるようにもなりたいです。
AGCは、コアとなるガラス事業のほかにも様々な新規事業に取り組んでおり、会社全体の基盤技術を司る共通基盤技術部はそのどちらにも携われることが魅力です。これまで取り扱ったことのない材料やプロセスの評価に果敢に挑戦し、会社全体として将来にわたって活用できるような基盤となる技術の開発をこれからも積極的に行っていきたいと考えています。
<プロフィール>
松岡瑞樹
2010年入社。創造理工学研究科 地球環境資源理工学専攻。学生時代は層状無機化合物と有機化合物のハイブリッド材料、新規光触媒材料の合成などを研究。現在はチームでマネージャーを務める。
中島あゆ美
2022年入社。理工学研究科 総合デザイン工学専攻。ものづくりの上流にある素材に携わることに魅力を感じ、AGCに入社。大学院では精密ナノ加工研究室に所属し、金属表面へのレーザによる微細加工を研究。
(※所属などはすべて掲載当時の情報です。)
関連記事Recommend
-
理系の職種紹介vol.10 研究支援ソフトウェア/ソリューション営業の仕事
株式会社レビティジャパン -有機合成博士が強力に推進する研究DX-
-
理系の職種紹介vol.9 家電の生産技術の仕事
日立グローバルライフソリューションズ株式会社
-
理系の職種紹介vol.8 化学メーカーにおける素材開発の仕事
DIC株式会社
-
理系の職種紹介vol.7 食品メーカーにおける製品開発の仕事
日清食品グループ グローバルイノベーション研究センター
-
理系人材が活躍!貴重な文化財を守る「保存科学」とは?
国立民族学博物館・日髙教授の仕事に迫る。 -
科学の眼差しで描くイラストレーション
「サイエンスイラストレーター」の仕事拝見〜北海道大学CoSTEP 大内田美沙紀先生〜
-
理系の職種紹介vol.6 サイエンスコミュニケーターの仕事(資生堂編)
株式会社資生堂 ブランド価値開発研究所
-
アルコールがついても字が消えない!理化学系研究者の救世主、コクヨ“リサーチラボペン”開発担当者を直撃しました!
-
「卵アレルギーでも食べられる卵」を研究!卵研究とレシピ開発の強力タッグで、全ての人が安心して食べられる卵製品を届けたい
理系のキャリア図鑑vol.32 キユーピー株式会社 児玉大介さん、岩本知子さん
-
入社後の初仕事は研究所の立ち上げ!牛の尿の発酵液で環境課題を解決する 環境大善株式会社 加藤勇太さん
地方中小企業躍進の現場で活躍する理系人
リケラボ編集部より
ものづくりにおいて、製品の物性を評価する重要性は実際に仕事に就いてなくても想像しやすいですが、今回取り上げた、製造設備で使うものの物性についても厳密な分析・評価が必要なことは、言われてみると当たり前ですが意外と忘れがちだと思いました。
松岡さんによれば評価の仕事は、具体的な目に見える「モノ」として出来上がってくるわけではないため、「少し裏方寄り」の仕事だそうですが、「手法を作る面白さがある」とおっしゃっていたのが印象的でした。どんなに画期的な製品も、評価法が確立されていなければ市場に出せません。もてる知識と科学的思考を総動員しながら作り上げるとてもチャレンジングで魅力的な仕事だと思いました。
貴重なお話を聞かせてくださった松岡さん、中島さん、取材にご快諾いただいたAGC様、誠にありがとうございました。
化学業界の研究開発職なら
Chall-edgeにお任せ!
テンプスタッフの求人サイトジョブチェキに移動します。